如何用廢輪胎鋪路?
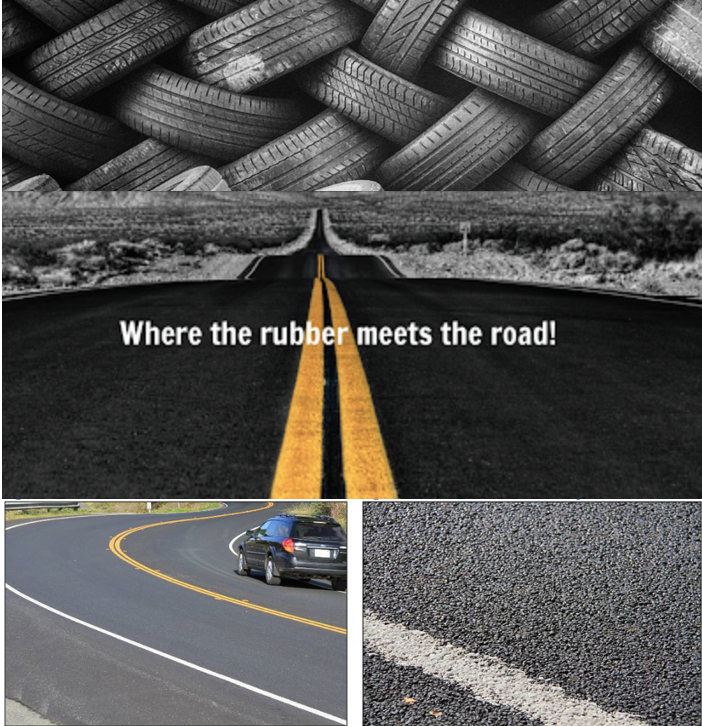
在美國路面工程界,橡膠瀝青的使用已經從被動協助處理廢輪胎堆積的環境問題,轉變成主動應用胎磨膠粉來提升瀝青路面成效的議題。
相關技術用語定義
- 添加胎磨膠粉(Ground Tire Rubber, GTR)改質的瀝青膠泥有許多好處,包括較能抗車轍變形、較抗滑、且能降低鋪面噪音,也能因減緩瀝青老化而使鋪面較慢變硬脆而更耐久;添加胎磨膠粉的所謂橡膠瀝青(Asphalt Rubber, AR)可用在開放級配瀝青面層,兼具提升雨天安全抗滑及降噪的雙重效果。但因工法特殊及未普遍應用,故常有許多混淆,有必要用基本定義來釐清「如何用廢輪胎鋪路?」
- 胎磨膠粉(Ground Tire Rubber, GTR)或橡膠屑改質劑(Crumb Rubber Modifier, CRM)是由廢輪胎經切割研磨處理製程而得的橡膠粉粒,再利用做為瀝青膠泥的改質劑。
- 橡膠瀝青(Asphalt Rubber, AR)則是依據美國材料與試驗學會(ASTM D8)的定義,是由瀝青膠泥、回收廢輪胎橡膠、及某些添加物組成,其中橡膠粒的百分比至少占全體混合重量的15%,且需在加熱拌合中與瀝青油產生橡膠粒的膨脹反應;橡膠瀝青的物理性質必須符合ASTM D6114 (橡膠瀝青標準規範)中表列的規定。
- 橡膠化瀝青(Rubberized Asphalt)則是胎磨膠粉添加量低於15%的另一種以胎磨膠粉改質的瀝青膠泥。
- 乾式製程(Dry Process)是指將胎磨膠粉以做為粒料的一小部份的方式,在熱拌廠將胎磨膠粉像粒料或填縫料般直接加入拌合機與其它組成材料拌成橡膠瀝青混凝土。
- 溼式製程(Wet Process)是指先將胎磨膠粉與瀝青膠泥在高溫下拌合並且反應一段時間,再噴入熱拌廠的拌合機內與其它組成材料拌成橡膠瀝青混凝土,或是直接噴撒在需處理的路面上使用。
- 工廠化橡膠瀝青(Terminal Blending of Rubberized Asphalt)則是將胎磨膠粉在煉油廠等級的油槽中與瀝青膠泥拌合反應成均質的橡化瀝青,再以油罐車運至熱拌廠的油槽中使用,這種工廠化橡膠瀝青的胎磨膠粉添加量有可能高於15%,也有可能低於15%,是由苯烯、丁烯橡膠、碳黑、及芳香烴等油類組成的均質穩定瀝青材料。
廢輪胎製成胎磨膠粉
現代輪胎由天然橡膠、合成橡膠、化學摻料、碳黑與矽、鋼絲、及纖維組成,如下圖所示。上個世紀初,天然橡膠取得不易且價格昂貴,橡膠製品中使用高達50%再生橡膠;但,自輪胎製造進入硫化橡膠及鋼絲加勁的高強耐磨耐久的現代製程,只能使用約2%再生橡膠;隨著汽車工業的發達,廢輪胎的產出量亦加速成長,由於輪胎不經生物分解腐化,棄置會產生許多問題,除了堆置造成景觀破壞外,又因質輕體積大,嚴重影響掩埋場的使用年限,若再加上蚊害病媒環境衛生問題、及易燃火災等危害,使得廢輪胎的資源化處理成為20世紀末的重要議題,且沿續至今。
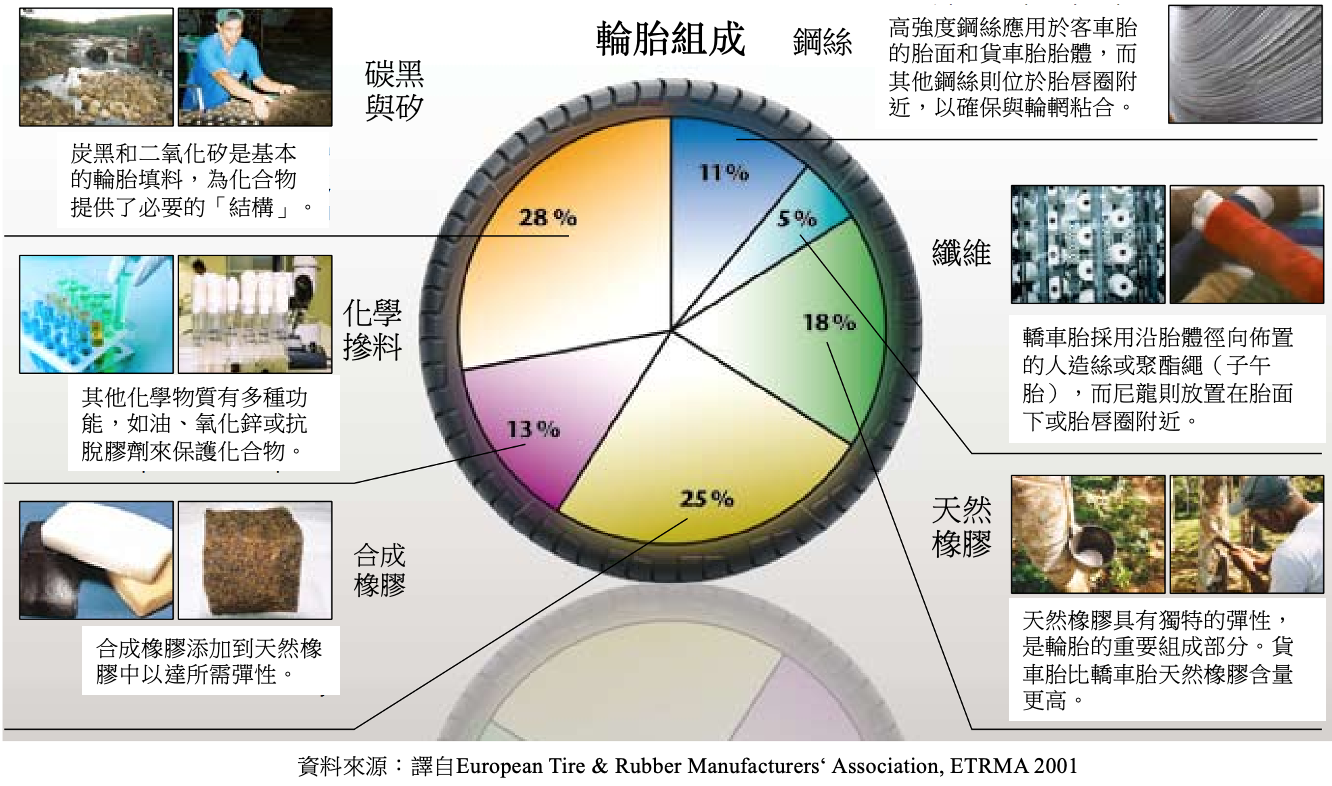
現代製程的胎磨膠粉是由高度品質控制產出的再生原料。下圖說明廢輪胎切割磨粉(造粒)的流程,大車胎一般會先抽離胎唇鋼絲,小車胎則直接餵入第一道切割成片(B),切割片再經細切且經磁吸分離出鋼絲與膠片,膠片再經細切篩分、分離鋼絲、及空氣吹吸除纖維,再依需求反覆研磨篩分、分離鋼絲、吹吸除纖維的製程而得到潔淨且高度均質的再生橡膠材料。製程中的鋼絲由煉鋼業回收,纖維目前則大都當垃圾焚化,一般製程產出15%鋼絲、75%胎磨膠粉、10%纖維。
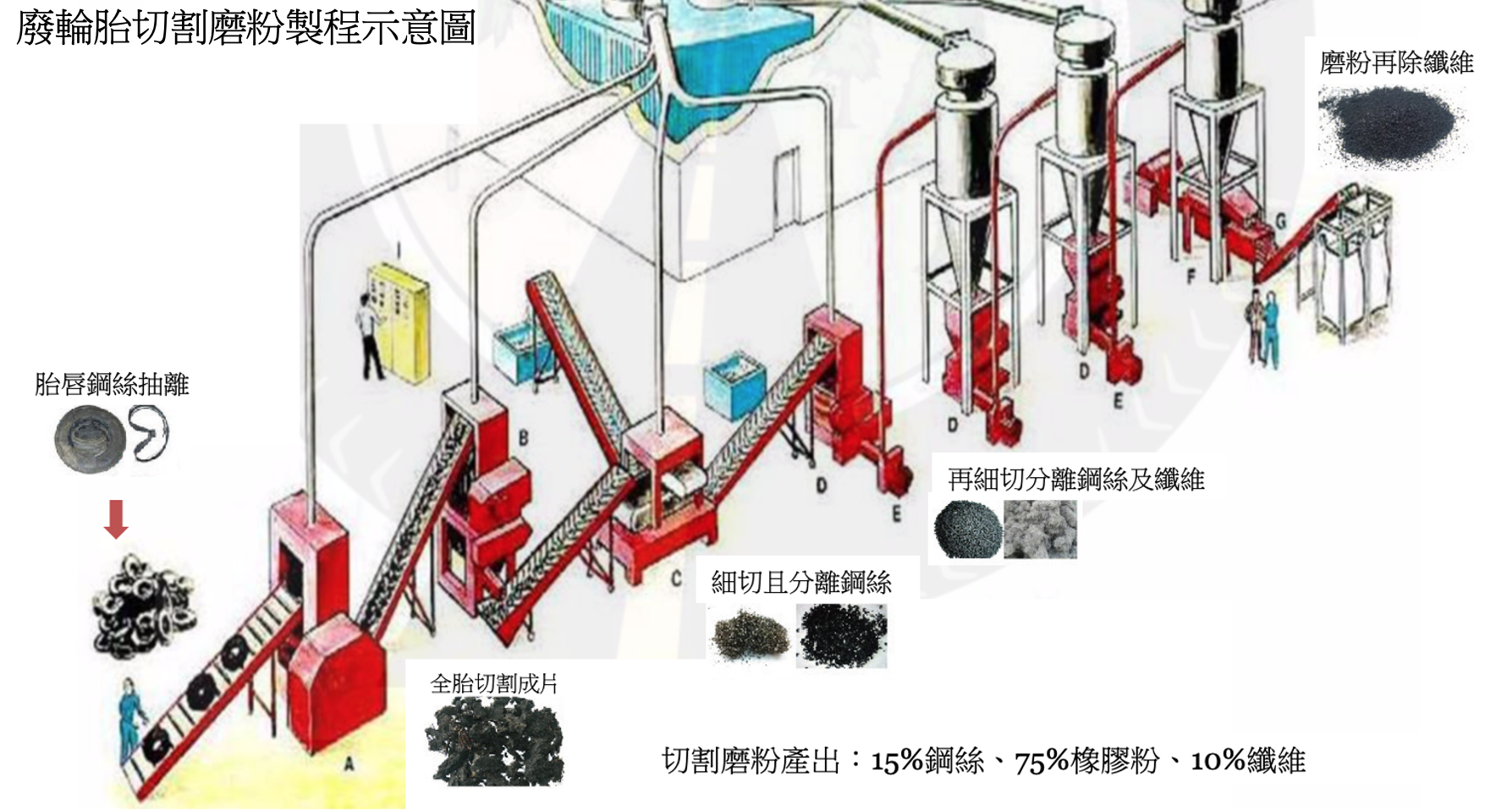
即拌即用橡膠瀝青
溼式製程的橡膠瀝青源於1960年代的亞利桑納州,在1978年出現好幾個橡膠瀝青專利;由於橡膠瀝青中的橡膠粒與瀝青只有「部份反應」(部份瀝青油成份溶入橡膠分子結構中使之膨脹),拌合溫度較高,且需減少混合粒料中的砂量來容納橡膠粒,故需與開放級配或是越級配搭配,不應用在一般密級配。用在越級配時因粗粒料形成的主架構具良好的抗變形能力,高瀝青含量展現的較厚瀝青膜提昇耐久性,而瀝青膜中含有的彈性橡膠粒給予很好的抗疲勞性。1993 未搭配適當經費補助的ISTEA強制使用條款引發爭議(詳參作者另文橡膠瀝青與工廠化橡膠瀝青在各國推動狀況);後遺症是這段期間因配比設計或工法錯誤而出現不少「橡膠瀝青的負評」。自1995年以後橡膠瀝青的產品及製程都沒有專利,公部門採用方便。
橡膠瀝青的品質控制需求主要有二項,其一是廢輪胎橡膠顆粒比瀝青重而沈澱造成析離,所以要在高溫狀態下持續攪拌使橡膠顆粒均勻懸浮在瀝青膠中;其次是若持續在高溫攪拌狀態下超過6或8小時,橡膠顆粒會因去硫化(de-vulcanization)及解聚合作用(de-polymerization)而失去彈性,故需即拌即用不能儲存,因此,成熟的橡膠瀝青需要採用特別的攪拌設備,在國外稱為橡膠瀝青攪拌機(AR Blender),如下圖所示,下表則為橡膠瀝青的優缺點匯整表。
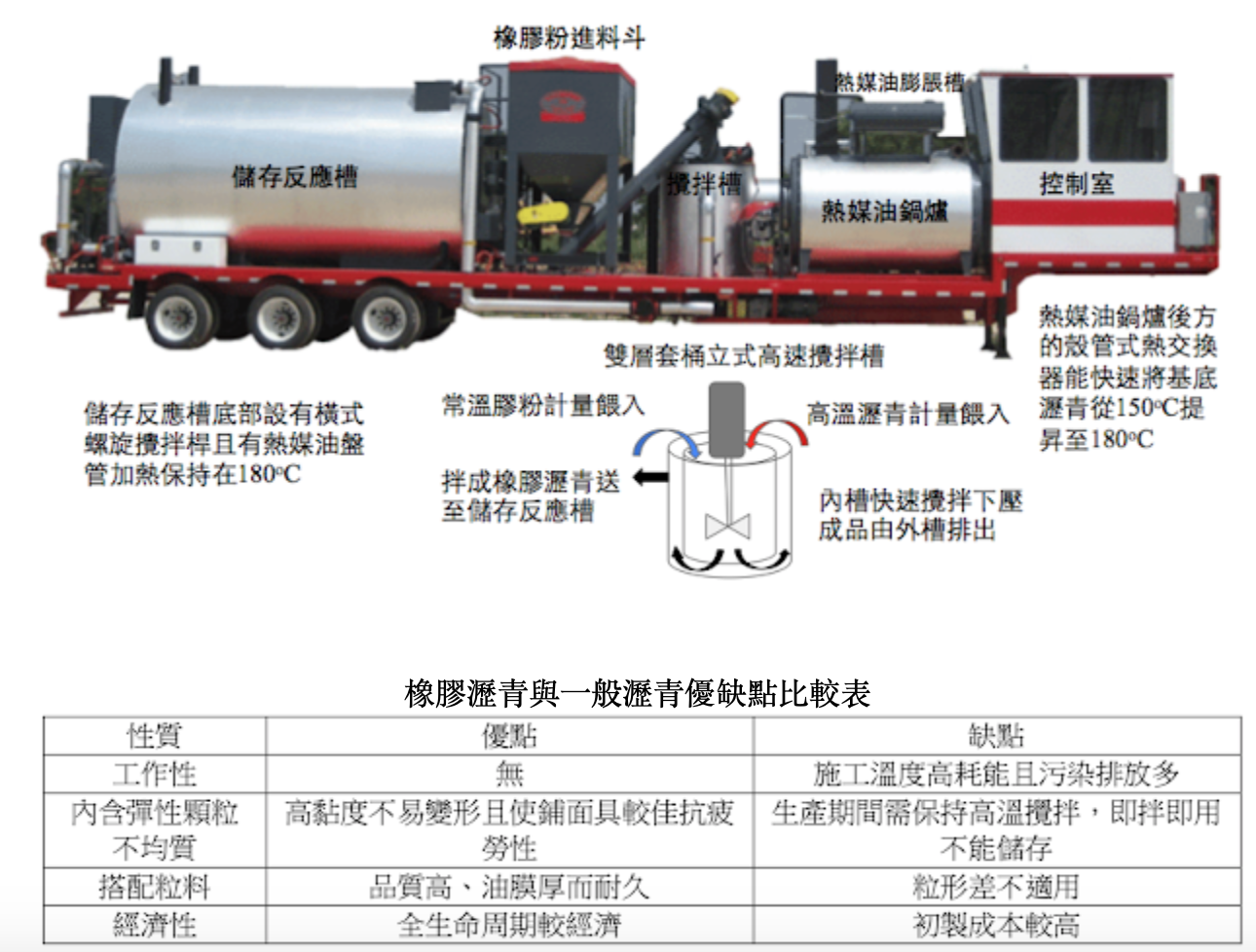
環保署自2012年重啟廢輪胎鋪路計畫,歷經與廢輪胎處理和瀝青拌合兩大產業的溝通,確認業者具有廢輪胎磨粉及橡膠瀝青拌製之能力,也有足夠的投資誘因,再租用國外成熟設備執行橡膠瀝青的產製試鋪,並透過環保署與交通部之間的「部會溝通」,確保公路單位採用此類鋪面的數量;近幾年來已陸續完成省道、快速道路、及高速公路的廢輪胎橡膠瀝青路面試鋪的工作,也在2017年發佈施工綱要規範,初步驗證國外先進國家採行的廢輪胎磨粉後鋪路的物質再利用方式,以廢輪胎橡膠瀝青鋪築的道路不僅耐久性佳、具有較好的抗變形及抗龜裂能力,且有降噪和抗滑的附加效果,是工程與環保雙贏的最佳選擇。
民國105年於國道1號高速公路頭屋路段北上122K+086~123K+550外側兩個車道鋪築開放級配橡膠瀝青混凝土成效良好;民國107(2018)年3月在台72線16K+000 - 23K+100西向側橡膠瀝青路面試鋪案,共長7.1公里平均寬11.3公尺,該案施工15天合計鋪築9,422公噸橡膠瀝青混凝土,依照公路總局第二區養護工程處的檢測告,該路段在施工前的平均國際糙度指數(IRI值,單位為m/km)外車道為3.30,內車道為2.99,施工後外車道平均為1.75,內車道為1.83,有效降低至公路總局要求的2.0以下;另鋪築完成時的平坦度驗收,以單車道200公尺為檢測段的高低平坦儀檢測的36個平坦度標準差值,平均值1.08、最小值0.80、最大值1.7,都達到一般公路2.4以下平坦度100%驗收的標準,驗證了廢輪胎橡膠瀝青的常規生產鋪築能力。
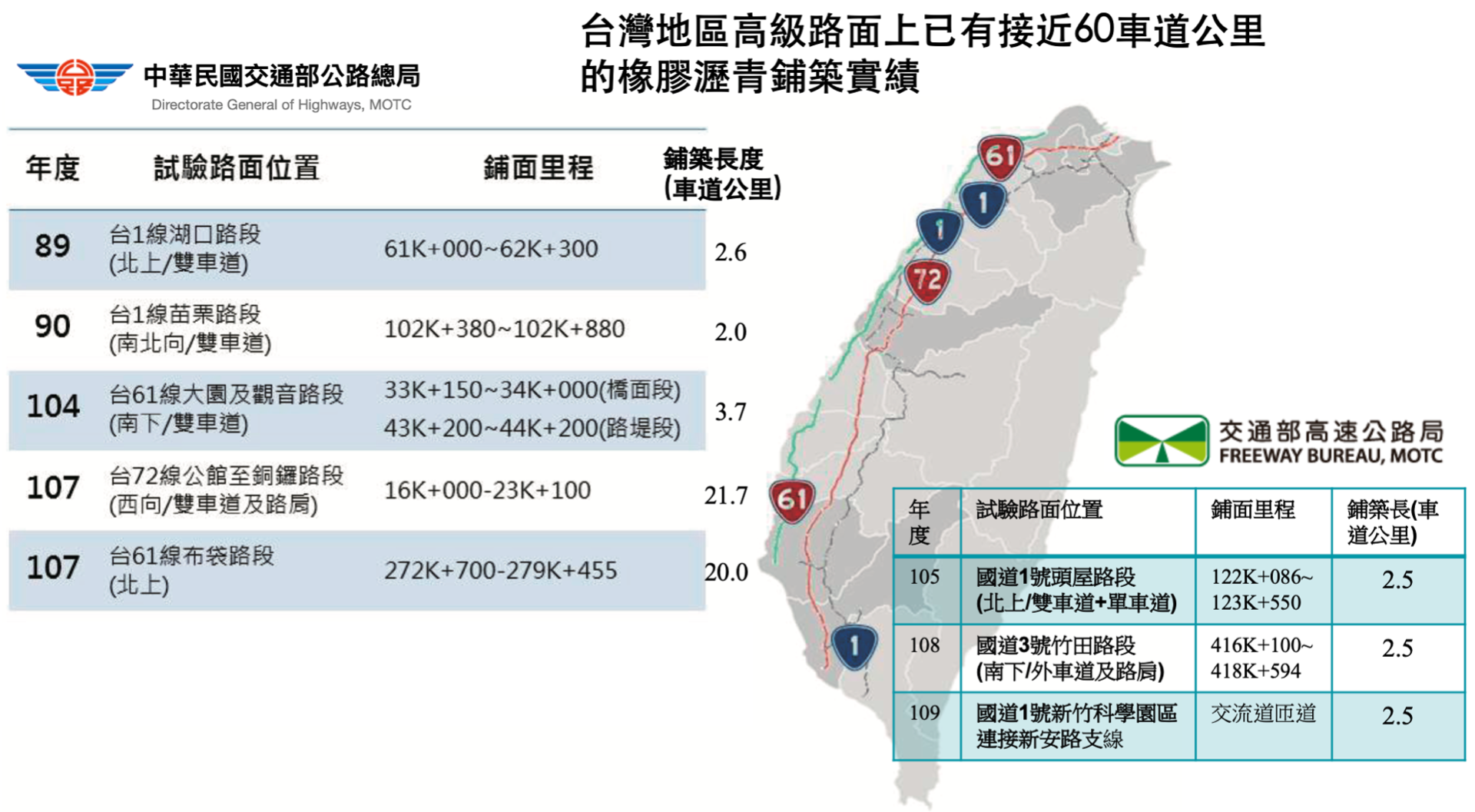
工廠橡膠化瀝青
工廠橡膠化瀝青一般用較細的廢輪胎橡膠粒,拌合較長的時間使呈均質狀,拌後用前不必攪動不會沉澱分離,可在煉油廠或專用工廠拌合,如下圖所示,可像一般鋪路瀝青或改質瀝青以油罐車運至拌合廠的油槽中使用,不必要有特別的橡膠瀝青拌製設備。這種橡膠改質瀝青的高溫黏度比橡膠瀝青低,且可以納入PG級規範(PG-TR)。橡膠瀝青與工廠化橡膠瀝青應視為兩種明顯不同的材料,比較橡膠瀝青與工廠橡膠化瀝青如下表所示。
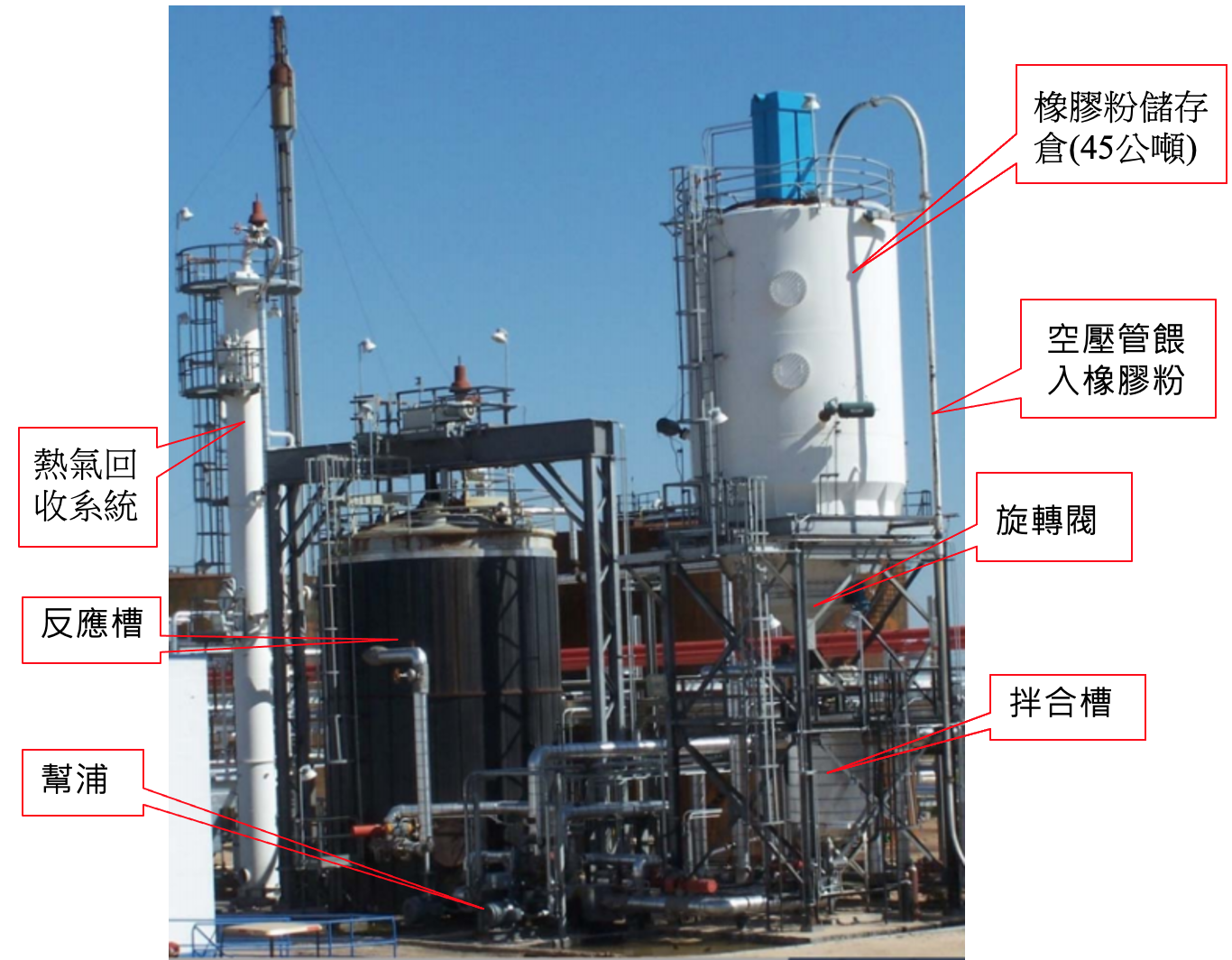
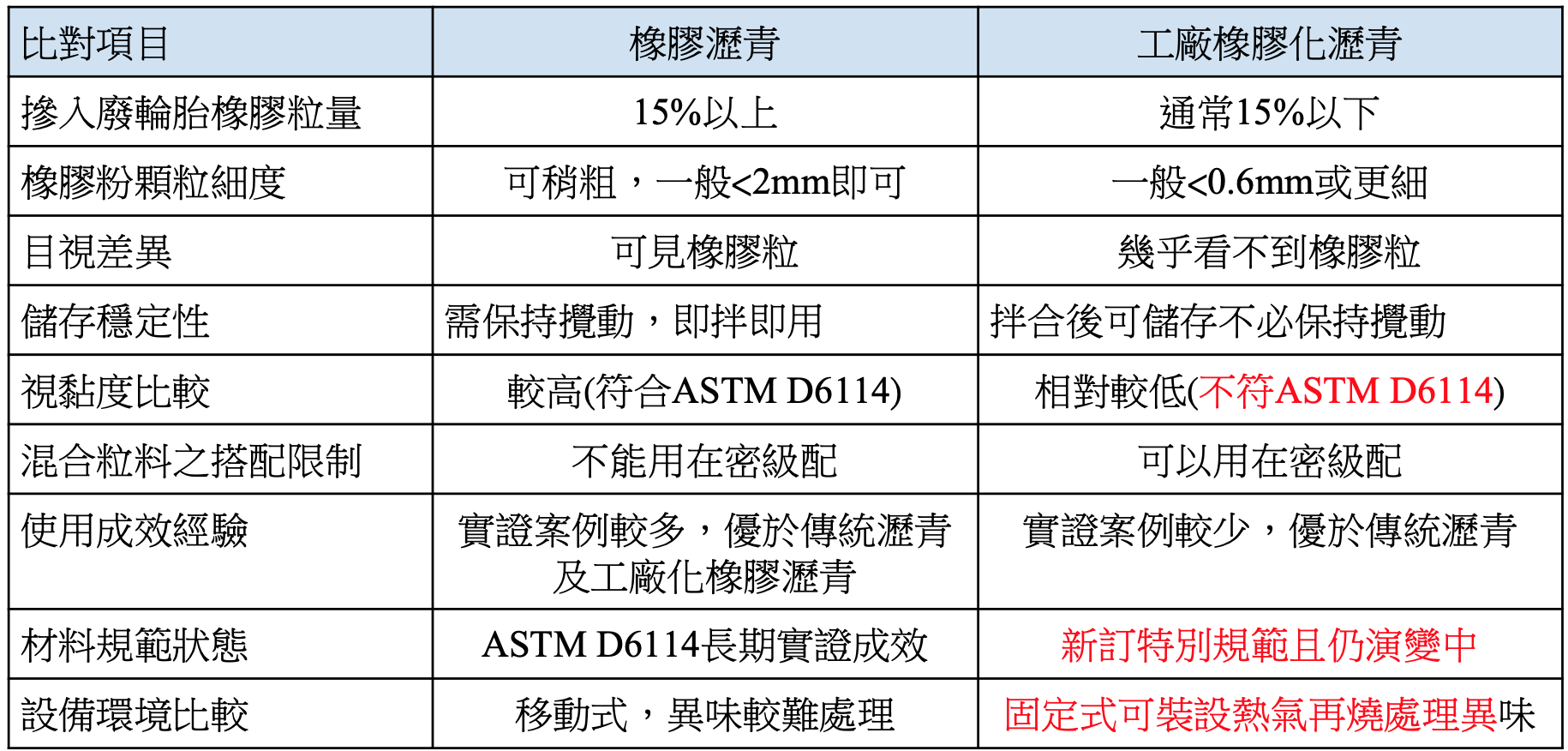
將橡膠瀝青「工廠化」源於想解決橡膠瀝青必需即拌即用的問題,再加上有些習慣使用高分子聚合物改質瀝青(Polymer Modified Asphalt)的工程師,甚至很不習慣橡膠瀝青可見廢輪胎橡膠顆粒,而視為「不均質材料」、「黏度太高很難處理」。將胎磨膠粉消化融入瀝青膠泥而成均質的瀝青材料,可以一般油罐車運至熱拌廠的油槽中儲存使用,不同於即拌即用的橡膠瀝青含吸油膨脹的橡膠粒呈不均質狀。利用高溫(有時加上高壓)及磨得較細的膠粉,加入比較多的量,其實是花費相當多額外的能源才做得到,而將膠粉消化融入瀝青膠泥後拌入瀝青混合料中,不再有原吸油膨脹彈性膠粒擁有的高稠黏度,裹在粒料表面的厚度也不再厚,既失去足以抗疲勞開裂的彈性,也不再有厚膠膜可提供的耐久性,也就是說為了得到所謂均質的材料而失去橡膠粒拌入瀝青混凝土中的好處。如果只取廢輪胎膠粉是二次原料,也能達到回收廢輪胎資源的環境效益。